by logisticsplus | Apr 25, 2017 | News
Global Supply Chain Control Towers are gaining interest among organizations that need greater visibility and control within their increasingly sophisticated supply chains. In a recent Capgemini Consulting report, a supply chain control tower is defined as a central hub with the required technology, organization and processes to capture and use supply chain data to provide enhanced visibility for short- and long-term decision making that is aligned with strategic objectives.
Supply chain towers are often an important component to 4PL supply chain solutions as companies realize that mastery of their supply chain must become a core competency to remain competitive. Although visibility within the supply chain is often a significant driver, the supply chain control tower must go beyond visibility to provide integrated transportation and logistics solutions and global trade compliance services. These services must be configured to support the needs of business units and the key fulfillment attributes of a product-line.
The value of having one global supply chain system and standardized processes gives companies the flexibility to plug in new transportation and logistics providers as needs change, or quickly assimilate new businesses. The control tower reduces the risk of getting locked into using an external provider’s system, and changes the balance of power. Control tower managers have the visibility and data-driven analysis of service levels to objectively manage each provider. Similarly, new businesses and product-lines can be plugged in with standard interfaces and highly configurable processes.
Logistics Plus has significant experience creating and managing global supply chain towers for a number of clients. We take a very customized, yet dedicated approach to configuring and integrating the control tower into each client’s supply chain. The two illustrations shown below are examples of control towers we have implemented for two very different companies (click to enlarge). One is a global energy company, and the other is a leading co-working space provider. As shown in the examples, the first company’s supply chain required multiple regional control towers to ensure visibility and control of logistics across multiple regions. In contrast, the second company required one primary, centrally-located control tower to oversee everything from procurement to warehousing to final deliveries.
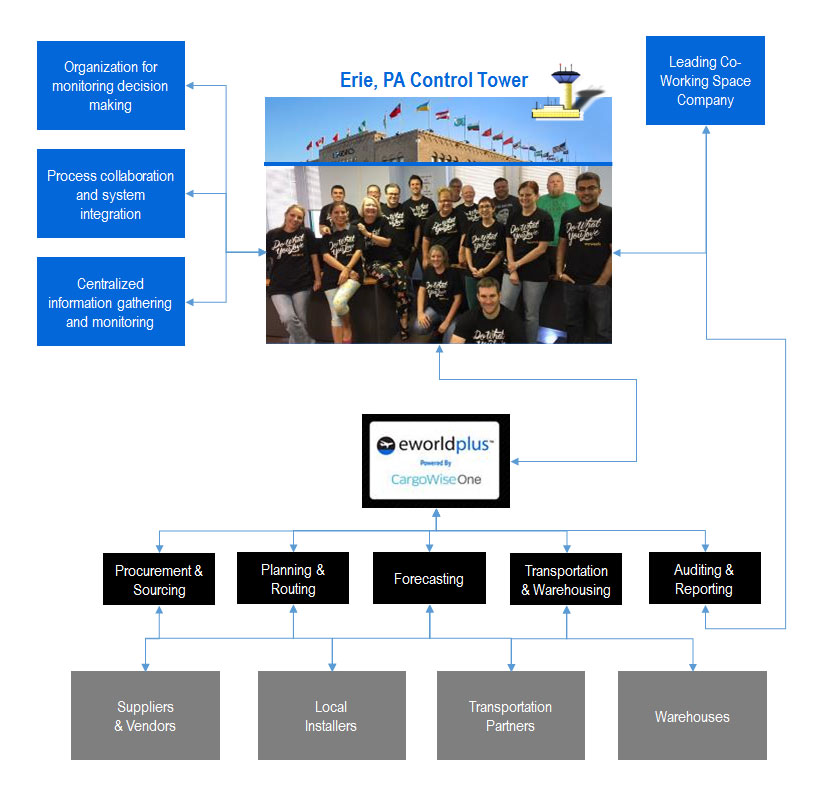
If you’re looking for greater visibility and control within your supply chain, with an experienced 4PL partner that uses a very customized and dedicated approach, please contact us. We’d love to review your business challenge and discuss whether a global supply chain tower might be a good fit for your company.
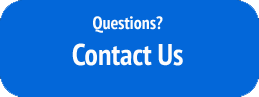
by logisticsplus | Mar 24, 2017 | News
Nick Hastreiter over at The Future of Everything recently posed the question “How will logistics change in the future?” to a number of successful logistics business leaders. Logistics Plus founder and CEO, Jim Berlin, was included in the article. Jim’s contribution, and the complete article, can be found on the The Future of Everything website by clicking the image below.
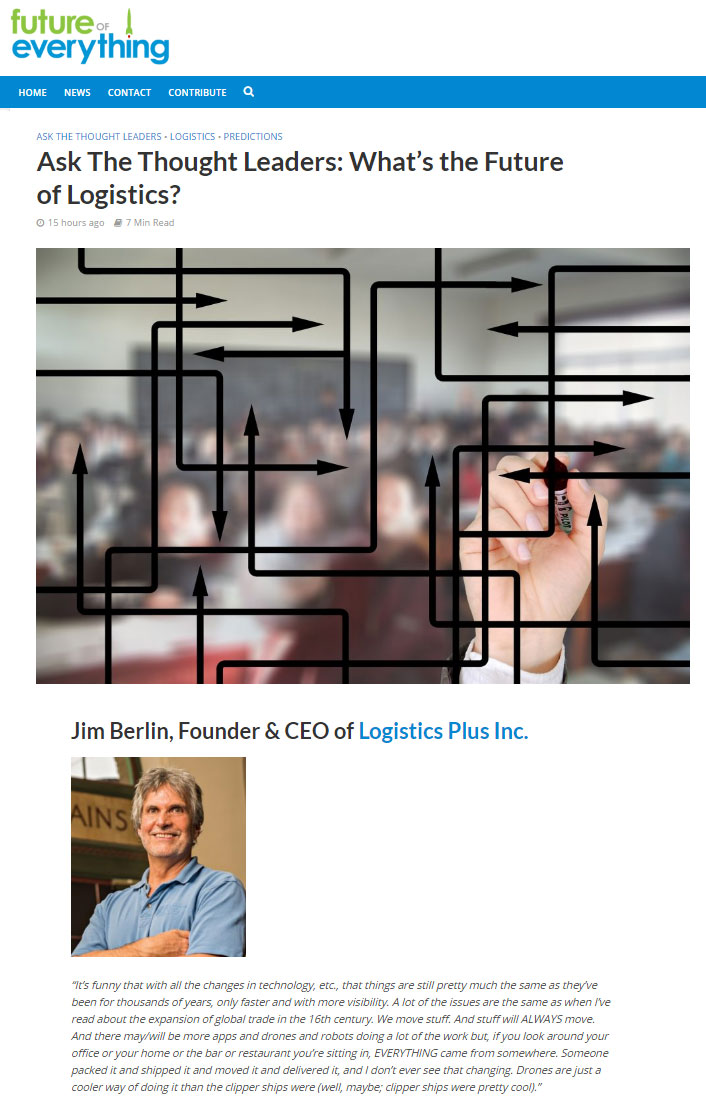
by logisticsplus | Mar 6, 2017 | Uncategorized
The Logistics Plus (LP) Middle East and Africa offices continue to enjoy fast growth and success within the region. Here are some updates from the LP team operating within this important area of the world.
Logistics Plus Dubai (UAE)
- LP Dubai primary team members: Suchit Sehgal, Siew Hua, Anjali Malik, Dhanraj Naidu, Ramesh Reddy, Reuben Alphonse, and Ronan Yuchitcho.
- Handling 100% of refurbished engine shipments for major power company. Additional shipments for Rwanda plant to begin Q3 2017.
- Moving shipments from UK, China and Germany to the Middle East for worldwide office furniture manufacturer. Quoting additional warehousing operations in Jebel and Dubai.
- Moved first shipment for a major painting and coatings manufacturer. Multiple more shipments are in the pipeline with support from LP Turkey.
- Moving shipments for cement company with plant located in Ras al-Khaimah.
- Bidding on multiple power transmission projects in Malawi and Ethiopia for major global power company.
- Moving agricultural company shipments from Ethiopia to Middle East with opportunity for 30-50 containers per month.
Logistics Plus Kingdom of Saudi Arabia (KSA)
- LP Jeddah primary team members: Raza Rizvi, Bakar Jafar, Omar Khalid, and Imran Ramzan.
- Handling over 1,000 40′ HC containers per month for major electric company.
- Secured small contract to support logistics for a marine cargo company.
- Hotel project in Saudi Arabia for a prominent leader in the agribusiness.
- Working with an association partner to move regular shipments from Saudi Arabia to UAE.
- Bidding on multiple projects in Dammam and Rabigh in support of local freight forwarder.
Logistics Plus East Africa (EA)
- LP Uganda primary team member: Julius Nyaika
- Bidding and handling various tenders for the United Nations (UN).
- Making in-roads with various companies in the oil and gas industry.
- Moving animal feed to and within Sudan in conjunction with a regional airport operator.
- Bidding on multiple projects in Kenya and Uganda in support of a major transport and logistics operator.
- Working with a Chinese petroleum company on multiple projects in East Africa.
Do you have supply chain or logistics needs in the Middle East or Africa? If yes, contact us and let our global experts go to work for you. Click the button below to complete our online inquiry form, or email suchit.sehgal@logisticsplus.com – our general manager for the Middle East and Africa
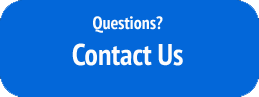
by logisticsplus | Nov 10, 2016 | News
What’s your most pressing logistics challenge? How much time and money are you spending on logistics? Are you measuring the total cost of your freight management activities? Through a “prepaid-and-add” approach, are your vendors charging you more for shipping than you realize for your purchased (inbound) goods? In addition to outbound and inbound freight charges, are you considering order preparation time, time-to-quote, personnel costs, owned-assets versus outsourced assets, inventory carrying costs, loss and damage claims, and insurance costs?
While these questions are not always easily answered, asking them is fundamental to successful P&L management. Outsourcing some or all of your transportation to a logistics company – one like Logistics Plus, which provides the required expertise, people, capacity, warehousing and IT systems – may help convert some of those high fixed costs into reduced variable costs.
Logistics Plus Inc. is a leading worldwide provider of transportation and logistics solutions. We have 20 years of experience helping companies, both large and small, reduce transportation expenses and improve their supply chains. General Electric (GE), one of the largest and most successful companies in the world, was our very first customer. Today they top a list of diverse companies that span manufacturing, retail, solar, energy, aviation, food and beverage, and many other industries.
We’ve been named one of the fastest-growing transportation and logistics companies in the country by Inc. magazine; we’ve been recognized as a top employer based in northwestern Pennsylvania; Transport Topics magazine named us a top 50 freight brokerage firm; SupplyChainBrain magazine named us a 2015 Great Supply Chain Partner; and this year Supply & Demand Chain Executive magazine recognized us on their SDCE 100 list for completing a top supply chain project.
If our services are good for companies like GE, we think there’s a good chance they’ll be good for your company too; which is why we we invite you to learn more about our solutions. But what really sets us apart is our people. We’ve developed a reputation as being the “can-do” company. Our people put the “Plus” in logistics by doing the big things properly, and the countless little things, that together ensure your satisfaction and success.
As a possible first step, tell the experts here at Logistics Plus your most pressing logistics challenge, and we’ll use our passion for excellence to go to work and design a solution that’s customized for you and your business.
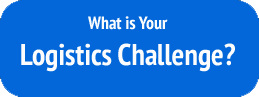
by logisticsplus | Sep 9, 2016 | News
Many recent articles and white papers have been discussing the emerging trend of nearshoring in Mexico. Thanks to rising costs in China, delays and disruptions to transpacific shipping routes, and logjams at United States western seaports, many manufacturers are looking closer to home for their sourcing needs. For many of these companies, Mexico – the third largest U.S. trade partner – has become a cost-effective alternative.
According to a recent manufacturing study published by a reputable global research firm, some 46 percent of respondents have already engaged in a plan to nearshore within the next five years. Of those companies, 63 percent say Mexico is the leading candidate, citing lower transportation costs and improved speed-to-market. As a result of increasing demand, truck and rail traffic between the U.S. and Mexico set record highs for volume and freight value, in 2014 according to the U.S. Bureau of Transportation Statistics.
Being closer to the U.S. market by nearshoring in Mexico provides companies with a number of benefits, including:
- Proximity. A shipper can move freight from Mexico to the U.S. by ocean in 48 hours, and by truck within a few days or less. By contrast, shipping a container from Asia to the U.S. could take up to six weeks to deliver. Another consideration is that operating in similar time zones creates opportunities to strengthen collaboration between U.S. companies and their Mexico counterparts.
- Trucks and Rails. More than 1.37 million trucks crossed the U.S./Mexico border in the first quarter of 2015, up almost 3 percent from the prior year. Also, shippers now have more reliable and seamless intermodal service options between the U.S. and Mexico, which can offer a 15- to 20-percent cost advantage over trucks alone.
- Labor. Unlike a decade ago when Mexican labor costs were reportedly 60 percent higher than those in China, today they’re on par or lower. Mexican companies have also transitioned from simple assemblers of products to exceedingly sophisticated manufacturers.
With an abundant labor pool, lower wages, low energy costs, and simplified truck and rail transport, including intermodal operations, Mexico has emerged as a nearshore alternative to overseas manufacturing. Companies unfamiliar how best to optimize their U.S./Mexico supply chains through the use of effective cross-border transportation and warehousing can contact the experts at Logistics Plus for help. We have been managing logistics between the U.S. and Mexico for nearly 20 years, and we recently celebrated our 10th anniversary for operations in Mexico.
The benefits of working with the Logistics Plus cross-border logistics team include:
- Bilingual staff members on both sides of the border
- Proven experience and success on both sides of the border
- Competitive rates and contracts for cross-border transportation
- Full shipment visibility across the entire supply chain
- Customs clearance, global trade compliance, and NAFTA expertise
- Warehousing availability with Foreign Trade Zone (FTZ) activation
Please visit www.logisticsplus.com/Mexico to learn more or contact us using the button shown below.
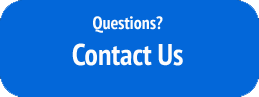