by logisticsplus | Aug 18, 2020 | News
In case you missed it, the Commodity Classifications Standards Board (CCSB) has published a new supplement to the National Motor Freight Classification (NMFC®). These changes became effective 8/15/2020. Some of the notable changes are listed below (thank you for the reminder from our friends at Southeastern Freight).
Boats or Boat Sections – Athletic Goods Group
- New items have been established for Boats, inflatable-24650 and Boats or Boat Sections-24670.
- Items 24540, 24660, 24665, 24666, 25000 and 25230 have been canceled.
Doors, including Mirrored Doors – Building Materials, Miscellaneous, Group
- The density scale for Item 34265 is going from 8 subs to 10 subs with classes increasing. Item 34265 has been amended to remove the restriction “other than rolling.”
- Items 34400 and 34500 changed “rolling” to “roll up”.
- Item 34330 has been canceled and moved to Item 34265.
- Item 34267 is amended to included mirrored doors.
Boxes, fiberboard, paper, paperboard or Pulpboard, combined or not combined with other materials
- New Item 29785 is established to incorporate many varieties of fiberboard or paperboard boxes. These will now be full-scale density items.
- Concurrently, Items 28920, 29205, 29240, 29250, 29285 and 29400 are canceled and have been moved to item 29785.
Foodstuffs, other than Frozen
- New items are established 72510 (Cocktail Mix), 72560 (Coconut), 73450 (Honey), 74095 (Molasses and other Syrups), 74310 (Popcorn, not popped), 74495 (Prepared Foods, such as pasta, noodles, rice, etc.) and 75400 (Vinegar).
- Items 72190, 72780, 73200, 74250, 74820, 73480, 74300, 75150 and 75180 are canceled and have been moved to these new Items.
- Additionally, 11 commodities have been removed from the viz listing in Item 73227 and moved to these new Items.
Broilers, Grills, Roasters or Stoves, cooking, outdoor type
- Item 25865 is amended to provide classes predicated on density with breaks at 6 and 10 PCF.
- Item 25860 is canceled with no further application.
- Items 25861, 25863, 25864, 25865 and 25866 have been clarified and simplified.
Bleachers or Grandstands
- The Grandstands Group IT-89800 is canceled.
- New Items 89790 and 89795 have been established to apply for all types of Bleachers and Grandstands with classes based on greatest dimension and density.
- Concurrently, Items 89803, 89805, 89810, 89813, 89816 and 89818 are canceled.
Curtain Poles or Rods
- Item 55190 is amended to a single class of 110.
Self-reactive materials – Hazard Class 4, Division 4.1 – Chemicals Group
- Item 46047 is established for self-reactive materials with classes predicated on whether or not the material is subject to temperature control requirements and by the self-reactive material type for the non-temperature-controlled materials.
Gates
- Item 86310 is amended to provide classes predicated on density, with breaks at 8 and 12 pcf. It is also amended by adding hallway and stairway gates for clarification.
Cans or Tubes, packaging, fiberboard, paper, paperboard or pulpboard
- New item 29860 is established for Cans or Tubes, mailing or packaging with classes predicated on density with breaks at 4, 6 and 12 pcf.
- Items 29030, 29760, 29820 and 29840 are canceled and moved to Item 29860.
Peanuts, other than raw
- Item 141800 for Peanuts, in shell, is amended to class 85.
- Item 141820 for Peanuts, shelled, is amended to class 70.
Pools, swimming or wading, other than in-ground pools
- Item 17050 is amended for clarification and to provide classes predicated on density breaks at 10 and 15 pcf.
Irons, Electric
- Item 62285 is amended for clarification and simplification, and class 125 is assigned.
Booths, paint and varnish spraying, or panels thereof
- New item 27900 is established for Booths, painting or varnish spraying, with classes based on greatest dimension and density.
- Items 27950, 27960 and 27970 are canceled and have been moved to new Item 27900.
Carriers or Racks, bicycle, motorcycle, motor scooter, mobility scooter or wheelchair, vehicle mounting, metal
- New Item 164075 is established with classes based on density breaks at 8 and 12 pcf.
- Item 164070 is canceled with reference to new Item 164075.
Burners or Burner heads, gas appliance
- Item 25885 is amended to provide classes predicated on density, with a single break at 9 pcf.
Workbenches
- New item 82250 is established for Workbenches with classes predicated on density breaks at 6 and 10 pcf.
- Items 79920 and 79930 are canceled.
Corrosive Materials – Hazard Class 8
- Item 44155 is amended to assign classes predicated on the DOT-assigned Packing Group.
Cesspools and Floor Drains
- New item 51130 is established for Floor Drains with classes based on a density break at 12 pcf.
- Item 50810 is canceled.
Blackboards or Chalkboards, NOI; Corkboards or Tackboards or Whiteboards, Dry Erase Boards or Markerboards
- Item 23701 is amended to specify additional packaging requirements only.
Pesticides, NOI
- Item 155050 is amended to remove the “bomb burst” symbol, add language further restricting the item’s application to materials not required by the DOT to bear a Hazard Class or Hazard Division label.
Obsolete Items
- Filler, arm rest , Item 18700 is canceled.
- Forms, arm rest, Item 18720 is canceled.
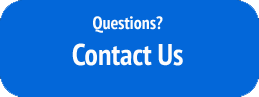
by logisticsplus | Jul 21, 2020 | News
As a freight broker/intermediary, Logistics Plus has no legal liability for loss and damage claims that occur as a result of carrier services we source for our customers; although we do offer to assist our customers with the processing of freight claims. No one likes to deal with missing or damaged goods or filing freight claims, but sometimes it happens. Here are six common types of freight claims.
- Damaged Claim – If physical damage to your shipment packaging is visible as noted by your consignee on the delivery receipt (or proof of delivery, POD), you can file a damage claim. Typically, you have nine months to submit a claim for visibly damaged goods. With proper evidence, the carrier will most likely refund a portion of your shipping costs. However, you’ll have to pay your freight invoice upfront and get reimbursed for any losses when the claim is processed.
- Concealed Damage Claim – When damage is concealed, that generally means it isn’t visible until after delivery, which means it was probably not notated on the POD. Concealed damaged claims are harder to prove. Most carriers only allow a five-day window to file a concealed damage claim (some even less based on each carriers’ rules tariff). If more than the allotted timeframe passes before you file, the carrier that handled your shipment will likely deny your claim. Including photos and any other evidence, you have with your claim will increase your odds of getting a partial refund.
- Shortage Claim – If your shipment shows up with a shortage and the consignee notates it on the POD, you can file a shortage claim. This can happen if the packaging is not intact and freight is missing. It can also happen if the amount of freight delivered doesn’t match what’s printed on the original bill of lading (BOL). Again, you typically nine months to file a claim. Expect to pay your freight upfront and then get reimbursed once the claim has been processed.
- Concealed Shortage Claim – Like a concealed damage claim, concealed shortage claims occur when a missing product is not noted on your POD, meaning it isn’t visibly evident that you’re short until after delivery. With concealed shortages, the packaging is usually intact, and it’s not obvious that freight delivered doesn’t match freight specified on the original BOL. Concealed shortage claims are difficult to prove, so you’ll often find that carriers push back. As with other concealed claims, time is of the essence. You only have five business days (or less) to file a claim.
- Refused Claim – Sometimes, a shipment delivers and it’s the wrong freight, the product is damaged, or the shipment is late. Consignees have the right to refuse part or all of shipment if they are unhappy with the condition of their freight. If your consignee refuses the shipment, it’s returned to the carrier’s delivery terminal. The carrier will contact you and ask what you want them to do with your shipment. Your options are to have it shipped back to you, have it sent to another address, or have it disposed of. In most cases, you will not have to pay your invoice.
- Loss Claim – A loss claim is a worst-case scenario because it means your entire shipment was lost by the carrier. This most commonly happens when shipment paperwork is separated from the freight. When this occurs, the carrier typically has a week to attempt to locate your freight. If they can’t find it, you shouldn’t be charged for shipping.
The carrier must acknowledge receipt within 30 days (49 CFR 370.5). Carriers must pay, decline, or make a firm compromise settlement offer within 120 days after receipt of the claim (49 CFR 370.9). The time period for commencing civil action cannot be less than two years from the date the carrier gives written notice to the claimant disallowing the claim (49 USC 14706e). Since there are legal time limits for filing and processing claims, you must obtain registered mail or other receipts indicating when you filed your claim.
Now that you understand the most common freight claim types, here are six common reasons why freight claims may be denied.
- Incomplete/Inadequate Documentation – When filing a freight claim, shippers should be sure to follow NMFC minimum documentation requirements. Probably the most common reason for a claim being denied is because of incomplete information and/or documentation. Logistics Plus offers help as to what documentation should be filed and can assist customers with the filing process.
- Mitigation – Per NMFC guidelines, it is the responsibility of a shipper to mitigate the costs of a claim to the least amount possible, which essentially means shippers are required to do their part to help minimize financial loss. Mitigation is usually done by selling the damaged item at a discount, selling it for parts or scrap, or by repairing the item rather than replacing it completely. If making repairs, the cost of repairing the item would be the amount filed for in the claim.
- Freight Charges Not Paid – Even if the freight charges are going to be refunded or credited in their entirety¸ per industry guidelines set by the NMFC, the freight charges for a shipment must be paid before a claim can be settled.
- Pallet/Piece Count – A bill of lading will typically denote having received “x” number of skids/pieces intact (shrink-wrapped/non-shrink wrapped) when a shipper performs their own load and count. When a carrier doesn’t perform the load and count, it’s considered that the number of skids/pieces tendered to the carrier is the quantity shipped, since they aren’t able to perform a piece count of the broken-down shipment before it was packaged to verify quantity. For example, a carrier is tendered 2 shrink-wrapped skids comprised of 25 individual boxes on each skid for a total of 50 boxes for the entire shipment, which the shipper shrink-wrapped and loaded onto the truck themselves. The carrier will likely mark the BOL as having received 2 shrink wrapped skids said to contain 50 boxes. When both skids arrive at the consignee and a shortage of 1 box is discovered, it’s difficult to prove that the shipment only contained 50 boxes to begin with. The shipper could have packaged the shipment with only 49 boxes by accident. The only thing the carrier knows for certain is that 2 skids were tendered, and 2 skids were delivered, as there was no opportunity for the driver to verify or count all 50 boxes, especially when skids are already shrink-wrapped when a carrier arrives for pickup.
- Clear Delivery – Establishing carrier liability without notation of damage on the delivery receipt can be difficult. In spite of what some shippers may think, writing “Subject to Inspection” on the POD does not serve as sufficient evidence that any specific damage has occurred, because it can create a scenario in which the consignee is the only witness to the discovery of the damage, which leaves reasonable doubt as to who was in possession of the shipment when the damage occurred.
- Act of God – Carriers are exempt from liability for things like hurricanes, floods, and fires, which are considered an act of God and beyond a carrier’s control.
You should be aware that all freight shipments come with some sort of “limited liability coverage.” This coverage is determined by the carrier and varies depending on the commodity type or freight class of the goods being shipped (more LTL carriers are going to limited liability by freight class). For the most part, carrier liability covers up to a certain dollar amount per pound of freight. It is not uncommon to find that the included liability coverage is less than the actual value of the goods being shipped. New goods liability limits generally run between $2 and $10 per pound; while used goods will typically be capped at $0.10 to $0.50 per pound. Also, special commodities also have released-value liability limits. So, if you are shipping a high-value shipment (new or used), you should consider some sort of additional shippers’ interest cargo insurance coverage.
Need freight claims help or are you looking for a freight claims management solution? Contact Logistics Plus – we’re here to help!
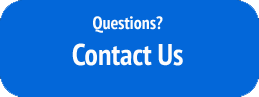
by logisticsplus | Jul 7, 2020 | News
Less-than-truckload (LTL) shipping can be somewhat complex and confusing. It is important for shippers to provide their LTL carrier – or 3PL/broker – with accurate bill of lading (BOL) information to avoid unexpected charges. Sometimes those surprises can come in the form of fees associated with overlength, linear foot, cubic capacity rules. The following is a quick primer regarding each of these three rules.
Overlength Rules (also called Extreme Length or Over Dimension)
Every LTL carrier has some form of overlength rules. For most carriers, those rules begin on any shipment containing one piece or item that is over 96 inches. For example (as shown below), UPS Freight has the following overlength fees: $90 for 96-143”; $125 for 144-239”; and $195 for 240-312”.
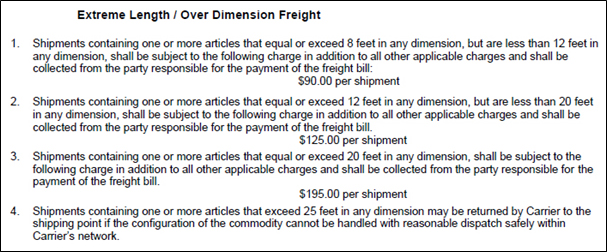

If you have two overlength items in the same shipment, most LTL carriers will only apply this fee once, but some carriers (such as R+L Carriers) will apply it for each overlength item. Overlength fees are applied as additions to the standard LTL pricing.
Linear Foot Rules
Most carriers no longer have linear foot rules (they instead rely upon their cubic capacity rules), but there are some that still have them in place. A linear foot rule will apply when the length of an entire shipment exceeds a maximum specified length. For example (as shown below), if a shipment is tendered to Dayton Freight that exceeds 15 linear feet with a density that is less than 22.5 PCF, it will be rated as if it was 1,250 pounds per linear foot instead of the BOL weight with standard LTL pricing.
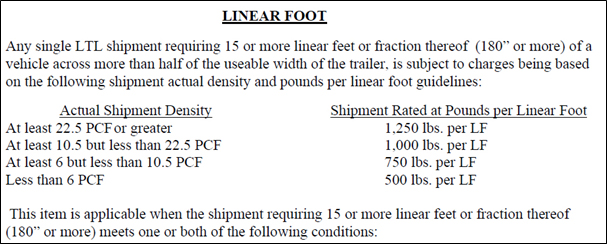

It’s important to note (and this is where it starts to get confusing), that this is only for shipments that do not have an overlength item – for those shipments, the overlength rules noted above would apply (although some carriers might rate it both ways and apply the higher rate of the two rules).
Cubic Capacity Rules (also called Density Rules)
Lastly, cubic capacity (or density) rules also come into play. For most carriers, these rules don’t apply unless a shipment is over 750 cubic feet and less than 6 pounds per cubic foot density. However, there are some carriers that have lower threshold rules as well (e.g., ABF also has a rule for shipments more than 350 cubic feet and less than 4 pounds per cubic foot density). An example of the cubic capacity rule for Ward Transport & Logistics is shown below.
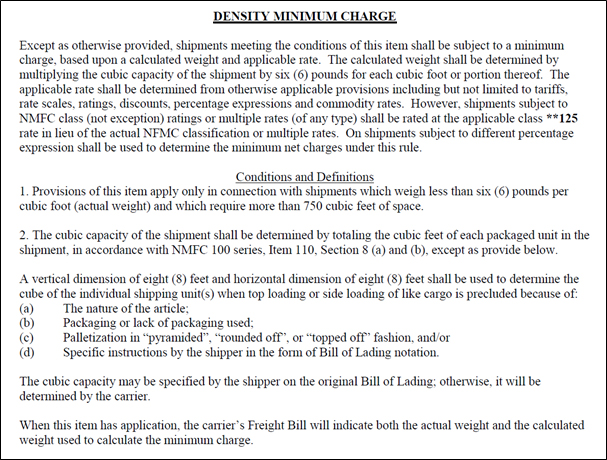

When cubic capacity rules apply, most carriers will automatically rate the shipment at a specified freight class (e.g., 125 in the Ward example) and they will artificially max out the weight according to a specified density rating and the rated dimensions (e.g., 6 pounds per cubic foot in the Ward example). The new cubic capacity rate will apply instead of the standard LTL pricing. For this reason, it is important to know the accurate dimensions and density of your shipment. Many carriers and 3PLs provide “density calculators” on their websites for this purpose; however, it is important to understand that most carriers will apply cubic capacity rules according to the space a shipment takes on its trailer (and not necessarily a shipment’s actual cubic feet). So a 48” non-stackable pallet will be considered to be 96” high by most carriers because they cannot load additional freight on top of the pallet. Likewise, a 52” wide pallet will be considered to be 96” wide since a second, standard pallet cannot be loaded alongside it.
As an additional example, a 5,000 pounds shipment of eight (8) standard (48x40x48) stackable pallets will equate to 426.7 cubic feet (192x80x96) and a density of 11.72 pounds per cubic foot. However, that same shipment, if non-stackable, would equate to 853.3 cubic feet and a density of 5.86 pounds per cubic foot. As a result, the latter shipment would most surely be “hit” with the carrier’s cubic capacity rule in lieu of standard LTL pricing.
Logistics Plus is here to help!
The bottom line is that LTL overlength, linear foot, cubic capacity rules are very complex and nearly impossible to quote accurately 100% of the time. That is why we recommend caution when quoting anything over 12 feet in length – and the logistics specialists at Logistics Plus are here to help if you have any questions regarding how to calculate density or apply any of the rules discussed above. We do incorporate the overlength fees and various other scenarios we can trust into our cloud-based TMS (called eShipPlus); but, as a general rule, we will not automatically quote any shipment that is over 750 cubic feet. For those shipments – or really for any shipment that is over 12 feet and/or 6 pallets – oftentimes we can quote those manually for our customers and obtain a much better “volume/spot” rate than standard LTL pricing. Drop us a line or give us a call if we can help you too!
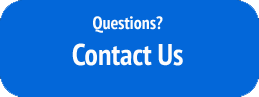
Interested in learning the difference between FTL and LTL shipping? Learn more.
by logisticsplus | Apr 27, 2020 | News
In case you missed it, the Commodity Classifications Standards Board (CCSB) has published a new supplement to the National Motor Freight Classification (NMFC®). These changes became effective 4/25/2020. A few of the notable changes are listed below (thank you for the assist from our friends at Estes Express).
- Foodstuffs group – A variety of changes here. The most significant being a new Item 134710 – Meats or Poultry, cooked, cured, dried, dry salted, pickled, smoked (NEW) or preserved, with or without other ingredients.
- Sub 1 – Less than 8 pcf – class 150
- Sub 2 – 8 but less than 12 – class 100
- Sub 3 – 12 or greater – class 70
- Organic Peroxides, Item 45463 .
- New classes for Types B, C D, E and F.
- Bathtubs, Showers, Shower Stalls, Hot Tubs or Spas, Item 158260.
- New classes dependent upon packaging and density. Six groupings. Item 158261 is canceled.
- 183100 TOBACCO, MANUFACTURED, GROUP: Articles consist of Manufactured (NEW) Tobacco, including Cigarettes, Cigars, Chew, Dip or Snuff, as described in items subject to this grouping.
- New Item which replaces Cigarettes and Cigars group #47760 and all related items. New items for the following
- Cigars, cigarettes or cigarillos. Three classes dependent upon density
- Kits, cigarette making – class 100
- Tobacco, smokeless, including Chewing Tobacco (Chew), Dipping(NEW) Tobacco (Dip), Snuff, Plug or Twist – Less than 12 pcf – class 100, greater than 12 pcf – class 77.5
- Tobacco, smoking, including Hookah, Shisha or Pipe Tobacco,(NEW) cut or granulated – Three classes dependent upon density.
- Household goods, Personal Effects or Military baggage – As modified, the description of item 100250 is amended by addition of the phrase “subject to Full Replacement Value (FRV) coverage,” and the last sentence of Note, item 100251, reading “This definition of FRV does not apply on motor vehicles, including automobiles or motorcycles,” is removed. These amendments are made for clarification and to better reflect the Defense Transportation Regulations.
- Saunas or Steam Baths, portable, – New Item 172740 which replaces 39220. New class is 175.
- Sauna or Steam Rooms, combined or not combined with showers – New Item which replaces 170650. New class is 150.
- Eyeglasses, Spectacles or Sunglasses, NOI – Item 57830 . Revised and regrouped under two subs. Sub 1 – less than 6 pcf , class 200, sub 2 – 6 or greater, class 125.
- Compressors, air, NOI; or Air Ends, NOI – Item 118100. Item 118100 is amended to provide density breaks at 8 and 12 pcf, with classes as shown. Sub 1 is amended to no longer apply on air compressors tendered “protected by a full-height fiberboard cap testing not less than 275 pounds and secured on lift truck skids or pallets.” New Note, item 118101 is established to provide additional packaging requirements.
- 82270 Metallic or Wooden Furniture, NOI, including Freestanding Panels, Partitions or Screens – Items 81550 and 82500 are canceled with reference to the full-scale density-based provisions of item 82270, and as modified, reference to freestanding panels, partitions or screens is added to the description of item 82270. Concurrently, Note, item 82501 is canceled with no further application.
- 153040 Envelopes, NOI, including Seed Envelopes or Packets, paper or paperboard. Item revised to class 77.5. Items 153030 and 153032 are canceled.
- 111655 Litter or Bedding, animal, in bags or boxes. Item revised from three density groupings to four density groupings. The density scale in item 111655 is amended by the addition of a break at 8 pcf, assigning class 175 to densities of less than 8 pcf. The noun “Bedding” is added to the description, while the references to “poultry” and “with or without additives” as well as the packaging reference to “drums” are removed.
- 35085 Partitions or Walls, interior, or Panels therefor, with or without integral (NEW) doors, – New Item which replaces 35040, Has Six density groupings and classes based on Length (exceeding or NOT exceeding 96 inches) and density. Old item was a simple class 70.
- Item 680, Sec. 9(a) – Amended to allow alternative methods of securement, while Sec. 9(b) provides specifications for how freight is to be secured on lift truck skids, pallets or platforms. Item 680, Sec. 7(c) and Package 107, which currently refer to Secs. 9(a) or (b), are amended accordingly.
- 114145 Air Humidifiers, NOI, with blowers or fans and Item 26580 Humidifiers.
- Item 26580 is amended by replacing “hot air house heating furnace” with “whole house,” and class 150 is assigned. Item 114145 is amended to provide classes based on packaging and density.
- 49795 Aprons, Coveralls, Laboratory Coats, Pants, Shirts or Clothing, NOI, disposable and 56530 Caps, Hoods, Leggings or Shoe Covers, disposable.
- Items 49795 and 56530 are canceled with reference to new item 56545, naming “Clothing, disposable, paper or nonwoven cloth, with or without reinforcement of other materials,” at class 150. The new item makes reference to Note, item 56714 for clarification. Note, item 49797 is canceled with no further application, and Note, item 49885 is amended accordingly.
- 40085 Marshmallows, NOI – Class changed from 85 to Class 175 on less than 7 pcf and 100 on 7 or greater.
- 53020 Coolers, draft beer dispensing (Kegerators), – Item 53020 is amended to assign class 175, and as modified, the item description is amended to read, “Coolers, draft beer dispensing (Kegerators), see Note, item 53021, other than hand portable, with or without mechanical cooling or freezing apparatus, drainboards or faucets (taps).” Also as modified, new Note, item 53021 is established to clarify that the item “Applies on coolers that dispense beer or other beverages from kegs.”
- Item 680, Sec. 6(a) – Amended to define “outer containers,” while Sec. 6(b) defines “inner containers.” Item 680, Secs. 6(c) and 6(d), and the title of the section are concurrently amended for clarification and uniformity.
- 61840 Extractors, juice (Juicers), countertop, – Amended from a single class 77.5 to provide less than 7 pcf, class 175, and greater than 7 pcf, class 100.
- 196000 Tires, rubber, scrap,. This Item canceled and replaced with 195720 Scrap, rubber tire, other than tires in their original form or shape, class 77.5.
- 156960 Netting, – amended to provide classes predicated on density breaks at 8 and 12 pcf, and the description is amended by removing the phrase “wound on cores, spools or tubes.
- 150970 Filter Stock – Amended to provide classes predicated on a density break at 8 pcf, and to remove packaging references to crates and to wrapped bales or bundles.
- 50312 Compounds, water cleaning or treating, bath, pool, spa or hot tub, – add restrictive language, and refer to new Note, item 50314, stating that the item does not apply on materials regulated by the DOT as hazardous and required to bear a Hazard Class or Hazard Division label. The new Note directs the Classification user to other items for classes applicable to such hazardous materials.
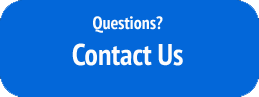
by logisticsplus | Mar 19, 2020 | News
Covid-19: Tips for Shippers & Consignees
As a result of the coronavirus (COVID-19) pandemic, many truck drivers are finding that it’s increasingly difficult to deliver freight. Some drivers are being denied into buildings, some are being required to fill out extra forms and bills are being left in the back of trailers. Listed below are 9 tips for keeping your loading docks healthy. (Click the banner or thumbnail image below to download a PDF copy of these tips)
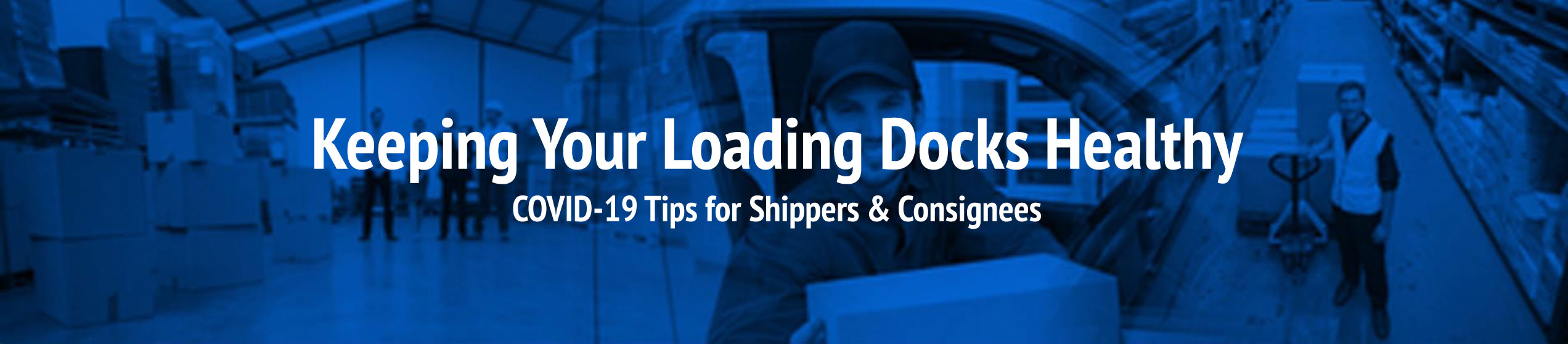

1) Ask Drivers and Dock Personnel to maintain the practice of “Social Distancing” and stand 6-10 feet away when interacting.
2) Make hand sanitizer, hand washing stations, disposable face masks, clean and unused pens readily available to drivers and dock personnel.
3) Limit loading and offloading, sort & segregation, routine inspection and count, and other dock activities to your own shipping/receiving personnel to avoid having drivers spend any unnecessary time on the dock.
4) Shippers – provide pre-signed copies of BOL’s and shipping docs on the freight, or in the back of the loaded trailer to limit interaction with driver.
5) Consignees – request that the driver themselves record the exact time of delivery, note any exceptions and obtain the name of the person who is accepting the freight. If a copy of the delivery receipt is required, request the driver leave a copy on top of the freight.
6) Many larger carriers have implemented their own forms of social distancing and rules of interaction for their drivers. Please be understanding and respectful of new policies drivers may be instructed to follow by their management.
7) Many shippers and consignees are asking drivers to stay in their trucks and stay out of buildings completely. This is a good way to help avoid contact all together. However…
8) Please consider that many regions have closed rest areas, public restrooms, restaurants, dining rooms, etc. Drivers need access to clean bathrooms and hand washing facilities now more than ever. Please help make sanitary basic restroom facilities accessible either inside your facility or by providing external port-a-potties and portable hand washing stations. The drivers that are serving you will appreciate it!!!!
9) Check the CDC website for updates: https://www.cdc.gov/coronavirus/
To read more updates and FAQ’s, including what Logistics Plus is doing to assist our customers during this pandemic, click here.
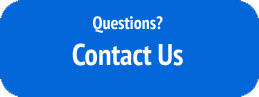
Page 5 of 12« First«...34567...10...»Last »